加工実績集 No.2
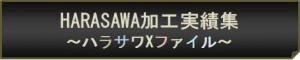
ご縁あってありがたくも弊社の新たなお客様となってくださったみなさま。本稿はそうしたみなさまへの技術案内となっております。お客様から見て「加工できそうなのに無理なモノ」、「無理そうに見えて加工できるモノ」をご紹介していく「HARASAWA 加工実績集」。本稿をお読みくださったみなさまがより弊社を便利に使っていただけるようになれば幸いです。
〜・〜・〜・〜・〜・〜・〜・〜・〜・〜・〜・〜・〜・〜・〜・〜・〜・〜・〜・〜・
【事例B】
材質:SUS409
寸法:φ42.7×板厚1.0t×全長250mm
条件:真円度公差±0.3㎜
〜・〜・〜・〜・〜・〜・〜・〜・〜・〜・〜・〜・〜・〜・〜・〜・〜・〜・〜・〜・
みなさまのイメージされるパイプと言えば連続造管の規格パイプなのでしょう。このためか弊社へご注文される際、製品の径がほぼ真円の精度で仕上がるようにお思いの方も少なくありません。今回採り上げた案件は材質SUS409のパンチングパイプ。一見、何の変哲もない案件と誤解されがちですが、板巻きパイプの特性上注意すべき点がございます。本稿ではこの板巻きパイプの注意点、「残留直線部と真円度」についてお話いたします。
① | 板厚の35~40倍くらいの径までが、ロール機での丸め加工の限界サイズとなる。 |
② | 加工可能な板厚でも、必ずワークの加工始端部と終端部に板厚の3~5倍の「残留直線部」というR(曲げ)のかからない部位が板材端部に残る。 |
どんな加工にも適用の限界があるものですが、鋼板をロール曲げで円筒形状に加工する場合上記の二点に注意せねばなりません。板厚が薄く、径の大きな品であればほとんど問題になりませんが、今回取り上げている事例のように丸め加工の限界サイズに近く、かつ板厚も1.0tを超えるものとなるとこの傾向は顕著に現れます。つまり連続造管の規格パイプと比較して、板巻きパイプにはサイズや真円度の面で弱点があるのです。
もし上記の問題を解決して真円度を追及する場合、代表的な方法として「①板材に予め曲げを施しておく端曲げ加工を行なう」か、若しくは「②パイプ形状に溶接後、金型で真円に成形する」手法を採ります。画像で製品のbefore→afterをご理解いただけるでしょうか。
![]() |
![]() |
![]() |
②の手法が最も高精度の真円度を出すことのできる手法となりますが、金型依存の加工のため、弊社でお客様のご要望に適うサイズの金型を保有しない場合は別途金型の製作が必要になること、成形の際、金型によって製品の表面に擦過傷が生じる恐れあることはよくよくご注意ください。
今回ご説明した板巻きパイプの残留直線部と真円度。ご理解いただけたでしょうか。もちろん弊社ではお客様がご所望であればロール加工以外の工法でお求めのサイズのパイプをご提供することが可能です。本稿がご講読くださったお客様のご参考となければ幸いです。
〜・〜・〜・〜・〜・〜・〜・〜・〜・〜・〜・〜・〜・〜・〜・〜・〜・〜・〜
~To be continued~