未然に防ぎたい行き違い ~径サイズの加工限度~
お客様とのやりとりの中で生じる行き違いをテーマにした本稿。第4回目は今回は『ロール加工の限度』についてです。弊社へご相談をよせてくださるお客様には、弊社で作る板巻きパイプのことを配管や構造用鋼管、若しくは板巻鋼管とほとんど変わらないものとのイメージの方が少なくありません。確かに同じ「管」ですが、加工原理の違いから製作可能な製品の径サイズに大きな違いがございます。今回はこの違いについて、一般的に用いられているパイプの加工法と比べた弊社の板巻きパイプの特徴を解説いたします。
円筒形状を得る加工法で最もポピュラーなのがロール曲げとロールフォーミングです。板巻鋼管の製作で用いられるロール曲げは、3本の芯金からなるロール機の手前2本の芯金の間に材料を挿入し、材料を奥の芯金に突き当てながら回転させることで曲げを得る加工法です。「端曲げ」と呼ばれる前加工が必要なこと、一度の加工で非常に緩やかな曲げしか得られないので何度も材料をセッティングし直したロール機に掛けなければならないことなどの弱点がありますが、板厚による加工制限を受けにくいため、肉厚な鋼板を大きなに曲げる際によく用いられます。
ロールフォーミングはコイル材をラインに直接送り、複数のロールダイスに通すことで幅方向から筒状に丸め込む加工法です。コイル材が徐々に丸め込まれていく様子を断面にすると花びらのように見えることからこの断面を「ロールフラワー」呼びますが、ロールフラワーをどんな風に設計するかは各社各様で、そのそれぞれにメーカー各社の素晴らしいノウハウが詰まっています。圧倒的生産能力と生産効率を誇り、高精度の管を大量に作ることができるため、世の中の規格サイズのパイプの殆どがこの方法で造られていますが、ご存じの通り径サイズは一定の種類しか造られていません。
これに対して弊社の板巻きパイプは、ウレタンロールを用いた曲げでパイプの製造を行なっています。この加工法はウレタンで覆われた2本の芯金を高い圧力で密着させ、ウレタンが沈み込んでできる曲状圧接面の間に材料を通すことで曲げを行なうもので、近似の3本ロールによる加工を比べ、端曲げなしに外観品質を損ねることなく、高い生産性で幅広い径のパイプを初期投資なしに造ることが可能です。
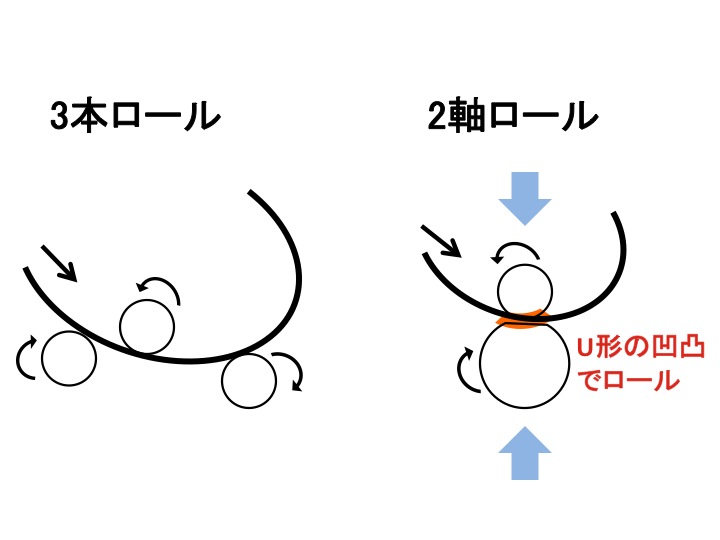
ロール曲げの大前提は管の直径が芯金よりも大きいこと。ただ、だからといって細い芯金を使えば細い管ができるというものでもありません。圧力を使って曲げを行なうウレタンロールのロール曲げは、細い芯金を使おうにも圧力に負けてしまい、芯金が弓なりに歪んで思うように曲げが得られない(鞍反り、中だれに近い成形状態になる)だけでなく、最悪芯金が折れてしまいます。厚い板厚の素材を曲げようとした場合も同様上手くいきません。材料自体の強度がロール機の加工能力を上回ってしまうからです。(材料の硬さ>ロール機の圧力)細くて長い管、板厚が厚い管の製作は私たちのもっとも弱点とするところ。加工可能なパイプの径は概ね板厚の35~40倍までが限度になることをご注意ください。
同じパイプでも、その加工法によりそれぞれのパイプの特徴は変わってまいります。板巻きパイプのことを「パイプより板金加工品に近いもの」とご理解いただければ幸いです。今号もご愛読いただき、誠にありがとうございました。